Engines have evolved and advanced over the years to meet EPA and customer demands. With these advancements the cooling systems and fluids they serve have had to evolve to meet the demands of increased temperatures, pressures and flow rates. Fleet managers and service technicians must review their preventive maintenance (PM) procedures and incorporate new strategies to achieve optimum efficiency, fuel economy and life out of the engine and fluids.
The function of the cooling system is to circulate the coolant through the engine to absorb and remove the heat. The cooling system is responsible for removing about 30% of combustion heat in heavy duty engines. If there is a deficiency in this process whether caused from a mechanical or maintenance issue, eventually engine failure will occur.
A deficiency in the cooling system will affect the engine, transmission and hydraulic system. Higher oil temperatures due to lack of heat transfer will lead to a reduction in the oil viscosity and oxidation. These systems will become less efficient and their life will be shortened.
Industry estimates that 50% of all premature engine failures or issues are due to a problem within the cooling system. Regrettably damage to this system can be difficult to see until damage has occurred unless you incorporate regular coolant maintenance practices and analysis to your PM schedule.
Properly maintaining this system can increase equipment uptime reducing loss in revenue due to unplanned downtime, reduce oil degradation, optimize coolant drain intervals, schedule downtime, increase engine performance and life and reduce maintenance costs.
To achieve optimal operating efficiency it starts with knowledge of the industry’s leading findings noted in the field that plague the cooling system. The most common issues found are:
Coolant Mixing
First and foremost, know the OEM fluid requirements. Engine manufacturers are very specific about what formulation of coolants can and should be used with their systems to achieve optimal life and efficiency. Some manufacturers are more specific than others as to what inhibitor package in the coolant is acceptable. Coolant formulations in the market are Heavy Duty Extended Life (NOAT ELC), Heavy Duty Nitrite Free Extended Life Antifreeze/ Coolant (OAT ELC) –, Conventional pre-charged Inorganic Acid Technology (IAO) and Hybrid Organic Acid Technology (HOAT). If the incorrect coolant is used warranty can be denied.
Issues that can occur when using the wrong type of coolant range from oil degradation, pitting, cavitation, corrosion water pump failure, freezing and boil-over. Using the incorrect formulation of coolant can also cause hoses to begin to leak which can lead to high-volume coolant loss and potential engine failure.
Many companies have more than one formulation of bulk coolant in their shops, this can lead to coolant mixing. Mixing coolant formulations will lead to dilution of the inhibitors from each of the formulations and leave the system vulnerable to corrosion and cavitation.
Looking at color is not a reliable indicator of what formulation of coolant is in a system. Review the manufacturer’s maintenance manual to determine acceptable coolants. It is possible to carry only one quality coolant formulation that will meet the OEM specifications for each manufacturer of equipment on-site. If coolant mixing is unavoidable it is best to change out new equipment when delivered to avoid coolant mixing.
Improper Top Off
When topping off the cooling system DO NOT overfill the system or top off with water only, always use a 50/50 premix coolant, allow the fluid to circulate completely throughout the system then check the coolant level and adjust if necessary. DO NOT mix coolant formulations.
Put It In and Forget It
The advancement of coolant technology with the development of organic acid technology coolants has made it easier to maintain the fluid. These coolants are more stable, do not require the consistent adding of supplemental coolant additives and transfers heat better but this does not mean you do not have to pay attention to this system.
Mechanical issues such as combustion gas leaks, air leaks, localized over-heating or hotspots or stray electrical ground issues can chemically affect and destroy the coolant and its inhibitors. In turn the chemically changed coolant can attack the metals and components in the system causing premature failure. A fluid cannot correct a mechanical issue but the mechanical issue can destroy the coolant making it unsuitable for continued use.
Neglecting the Cooling System During PMs
Regular schedule PM service is the optimum time to implement and perform a cooling system maintenance checklist. By adhering to a set of maintenance practices technicians become more engaged and aware of potential issues catching deficiencies in their infancy before damage has occurred. A good set of cooling system checks include:
- Inspect belt tension & condition, hoses, radiator, fan, fan clutch
- Check for leaks, stains or streaks around hose clamps or cylinder block and wet areas around the radiator and on the ground
- Check radiator for damaged fins, dirt or debris
- Inspect pressure cap – check pressure
- Check fan operation, clutch activation
- Check temperature variances with infrared heat gun
- Oil consumption or make-up oil (oil added)
- Check coolant level
- Perform appropriate field testing
- Pull sample for scheduled laboratory testing
Lack of Coolant Analysis Implementation
Many people understand the importance of oil analysis but neglect the implementation of having the coolant analyzed for mechanic or chemical issues. Studies have shown that by being reactive to unplanned maintenance or servicing issues can cost businesses three to four times more than having a preventive maintenance plan, but this plan must include all fluids. Analyzing your cooling system at a minimum of twice a year pays dividends on keeping the system operating at its optimal level, mitigating the effects on the oil systems and eliminating unscheduled downtime. No matter what coolant formulation is in use mechanical issues and contaminants can reduce the life and efficiency of your engine and other fluids. Only laboratory coolant analysis can pinpoint the issues before damage has occurred. Steps to implementing a successful fluid analysis program should include:
- Determine program goals
- Discuss any current equipment issues noted with oil and cooling systems
- Determine bulk coolants in use
- Formulate a workable plan
- Determine program moving forward
- Read and respond to the analysis report
- Compare coolant analysis with other unit fluid analysis results checking for issues affecting the other systems)
- Implement recommendations
- Following up
Our experts at Bureau Veritas can assist you with implementing a quality fluid analysis predictive maintenance program that will help reduce equipment and unscheduled downtime resulting in a return on your investment. For more information, check out our Coolant Analysis Services HERE.
Elizabeth O'Neil-Nelson
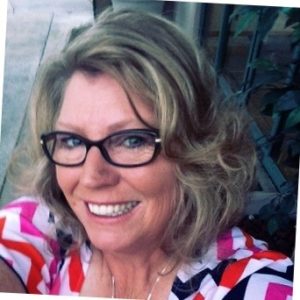