Optimizing oil drain intervals is a bit of a hidden gem within oil analysis. While oil drains are typically set according to time-based OEM recommendations, analyzing the condition of some key oil properties at those regularly scheduled PMs can provide the additional information needed to safely extend those intervals - by as much as 100%.
Although optimizing drain intervals can be applicable to any component, the highest savings is generally on engine oils. It is important to note that equipment under OEM warranty is not recommended for oil drain extensions unless approved and supported by the OEM. Partnering with your oil analysis provider, lubricant supplier and potentially also your filter supplier will usually provide enough information as to whether the engine is still in good health while optimizing the drain interval.
Fuel Consumption
Engines burning fuel at an abnormal rate are typically not good candidates for drain interval extension as the engine and the oil are generally working quite hard already.
Operating Conditions
Other factors, such as environment, also play a role. Extremely dusty conditions can potentially introduce abrasive materials which then require the oil to be drained prematurely to prevent any abnormal wear.
Case in Point
Customer: South African Mining Company
Extension Goal: 100%
Estimated Savings in Consumption: $449,000!
Introduction
A Bureau Veritas South African mining company conducted and documented a study on optimizing the diesel oil drain intervals of two Komatsu HD465 Rigid Dump Trucks in a fleet of 20. It was decided that the oils were to run to between 1200 and 1300 hours to factor in a 20 – 30% safety margin once rolled out to the entire fleet.
Oil sampling frequency was reduced to 1000 hours after the standard 500 hour drain, the filter differential pressures were monitored on a weekly basis to ensure there were no restrictions and fuel cleanliness was tested by particle counting to avoid contamination or any fluctuations in fuel consumption.
Testing & Analysis
The test slate included a number of parameters necessary to safely reaching the extended oil drain target of 1000 hours.
- Spectrochemical Analysis
One of the most common engine oil tests, Spectrochemical Analysis (typically by ICP or Inductively-Couple Plasma) shows trends in wear metals, contaminants and additives and can indicate a decline in both the condition of the oil and component health.
Fig 1. General Wear Graph – Iron level did not exceed 30ppm, which was below the OEM limit.
The additive content was measured more to indicate that the correct lubricant was being used and that there was no “lube mixing” during top ups.
Oil degradation through contamination is the most common reason for an oil drain. Silicon (dirt) must be attended to immediately.
- Viscosity is the most important physical property of an oil and can be influenced by many factors. An increase or decrease in Viscosity can determine if the oil is still within the recommended grade for the application. Viscosity, in conjunction with other oil analysis results, can provide a clear picture as to what is occurring within the component.
Fig 2. Viscosity Graph – Viscosity remained flat showing little deviation from the fresh oil to the oil at 1000 hours.
Infrared analysis measured such properties as fuel soot and oxidation. Fuel soot accounts for approximately 98% of the solid contaminants in today’s diesel engine oils making it a large factor in drain interval optimization. Soot is created by incomplete combustion of the fuel and enters the crankcase oil via ring blow-by.
Fig 3. – Soot graph – Soot levels remained acceptable throughout the study.
Fig 4. – TBN graph – There were no sudden increases in TBN throughout the study.
Base Number represents the amount of reserve alkalinity (or base) in the oil used to counteract the formation of acids during use. A decrease in BN indicates detergent additive depletion due to an increase in oxidation levels or the formation of acids.
Although these were the main tests monitored in the study, fuel dilution or water contamination were also evaluated. Fuel dilution may result in reduced viscosity to a point whereby the oil can no longer support the load required between moving parts and the equipment will be subjected to premature wear.
Water contamination in any lubrication system will detract from oil performance. Water can enter the oil system directly by leakage, from combustion, by condensation or through improper lubricant storage.
Cost Savings Calculation
The savings achieved by extending the drain interval, as calculated by the customer, are as follows:
“Savings estimated at R, 14,600 ($ 884.18 USD) per machine and savings for the entire fleet of 20 machines estimated at R 292,000 ($ 17,683.59 USD) per year. Applying this over a potential 40,000 hours, which translates into around 8.13 years, the savings are estimated at R 2,373,960.00 ($143,767.56 USD).”
“Considering a supplier change or cost reductions in the open market, the further cost savings are R 31,000 ($1,877.44 USD) per machine and for the fleet R 620,000 ($ 37,548.71 USD) per annum. Applying this over a potential 40,000 hours, which translates into around 8.13 years, the savings are estimated at R 5,040,600.00 ($ 305,276.53 USD).”
Conclusion
In summary, it is possible to safely extend the oil drain interval of an engine when monitoring certain parameters of representative samples sent to the laboratory accompanied by complete and accurate oil and component information to aid in the maintenance recommendation process.
Authored by: Deepak Deepnarain, CLS
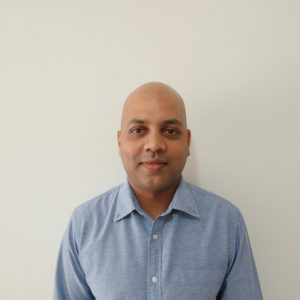